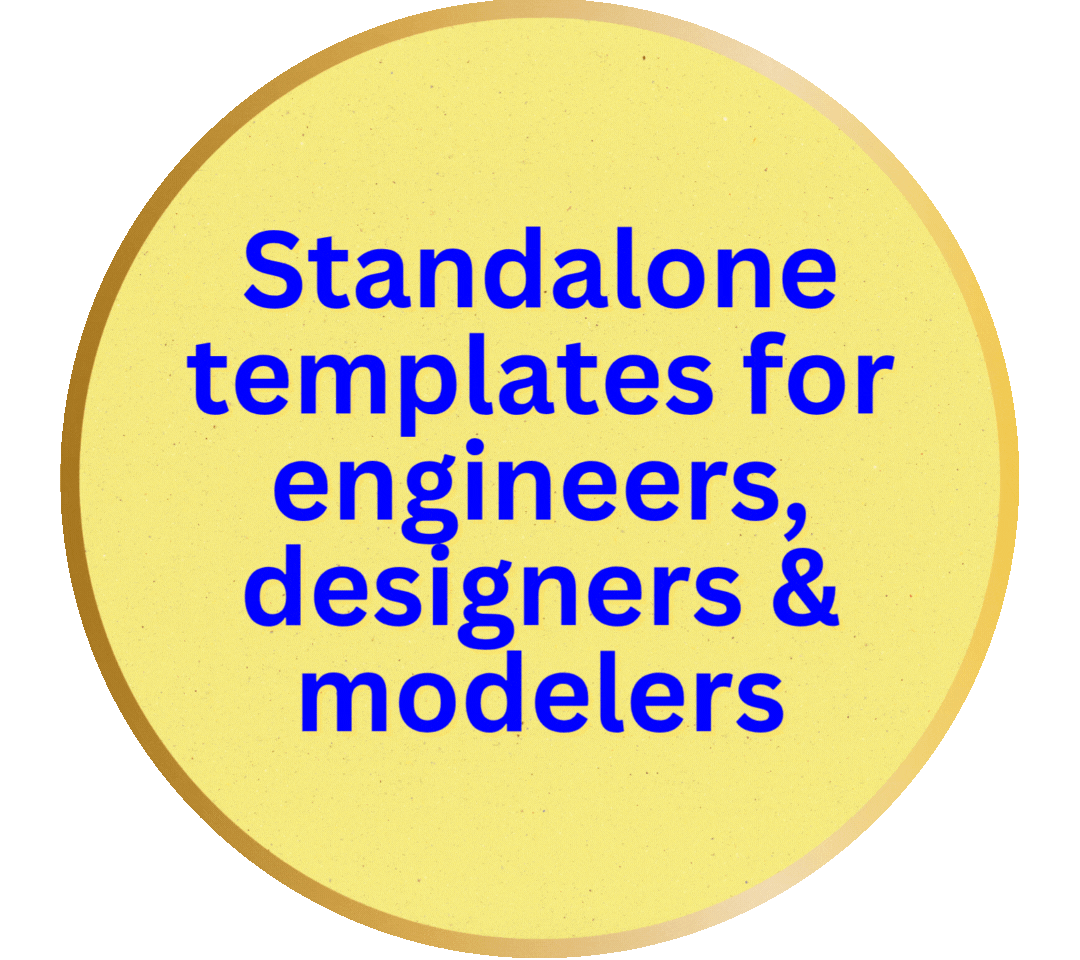
Where Structural Design Meets Cost Efficiency

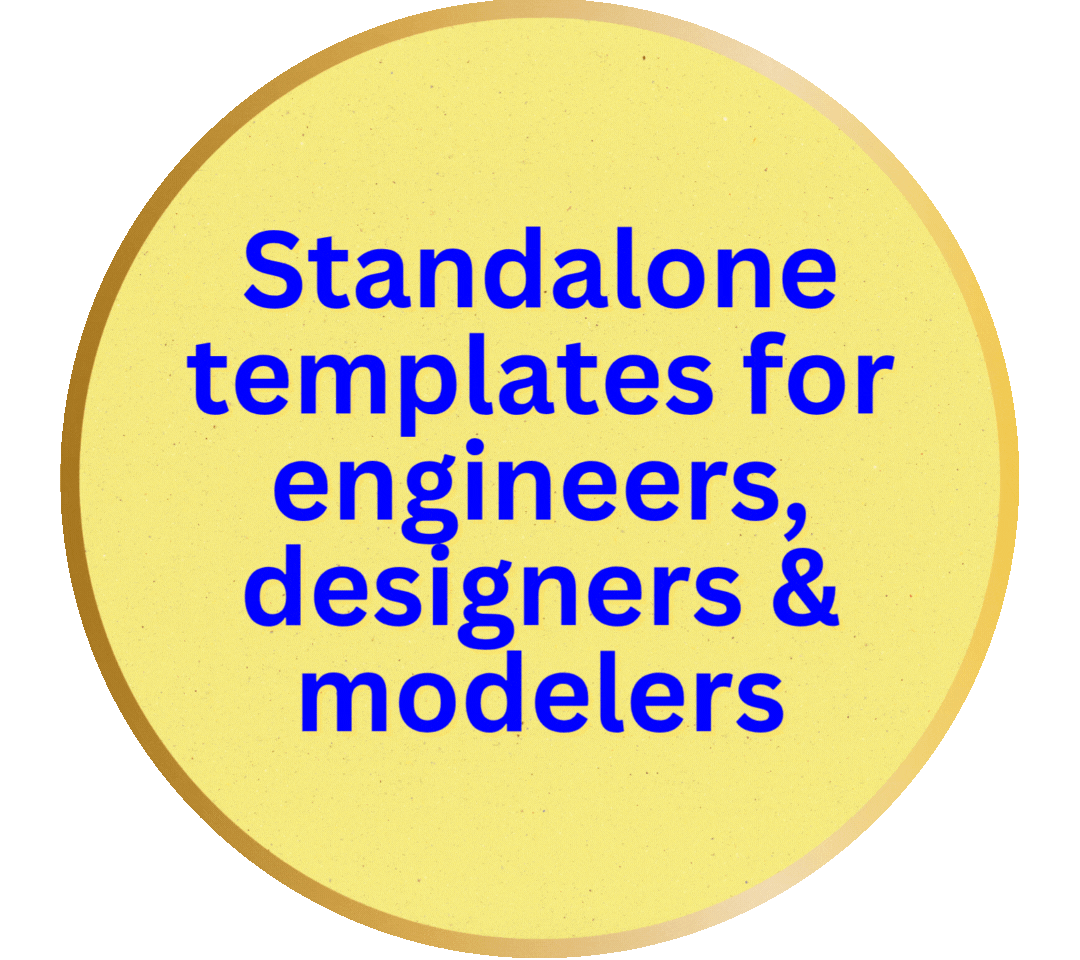

StrSof utilizes AI to identify the most cost-effective member size from the viable options, considering the provided material rates.
Unlike manual selection of critical load combinations in trial-and-error templates, StrSof leverages AI to do the selection for each design criterion.

StrSof Engineering Software
Choose The Best Structural Engineering Software For Your Organization


By using StrSof software for design of the ‘Spread Footing’, this user reduced foundation costs for a convention center, with just 26 spread footings, by over INR 1 million.
Cutting-Edge Design Tools
For Civil, Structural, and Mechanical Engineers
StrSof Software and automated templates have gained widespread acclaim in the civil and structural engineering community. They are currently highly sought after by practicing civil and structural engineers, as well as engineering students, research scholars, software programmers, and software developer firms. The following points elucidate the factors contributing to their widespread appeal:
- In contrast to trial-and-error design templates, these are characterized by a systematic approach.
- The design tools operate entirely on automation and do not necessitate user input derived from the outcomes of previous runs.
- The tools for member design yield the most cost-effective design outcomes.
- Each design tool has the capability to conserve valuable engineering man-hours.
- Manages up to 500 load combinations and 10 support joints in a single run (baseplate, spread footing and RCC pedestal).
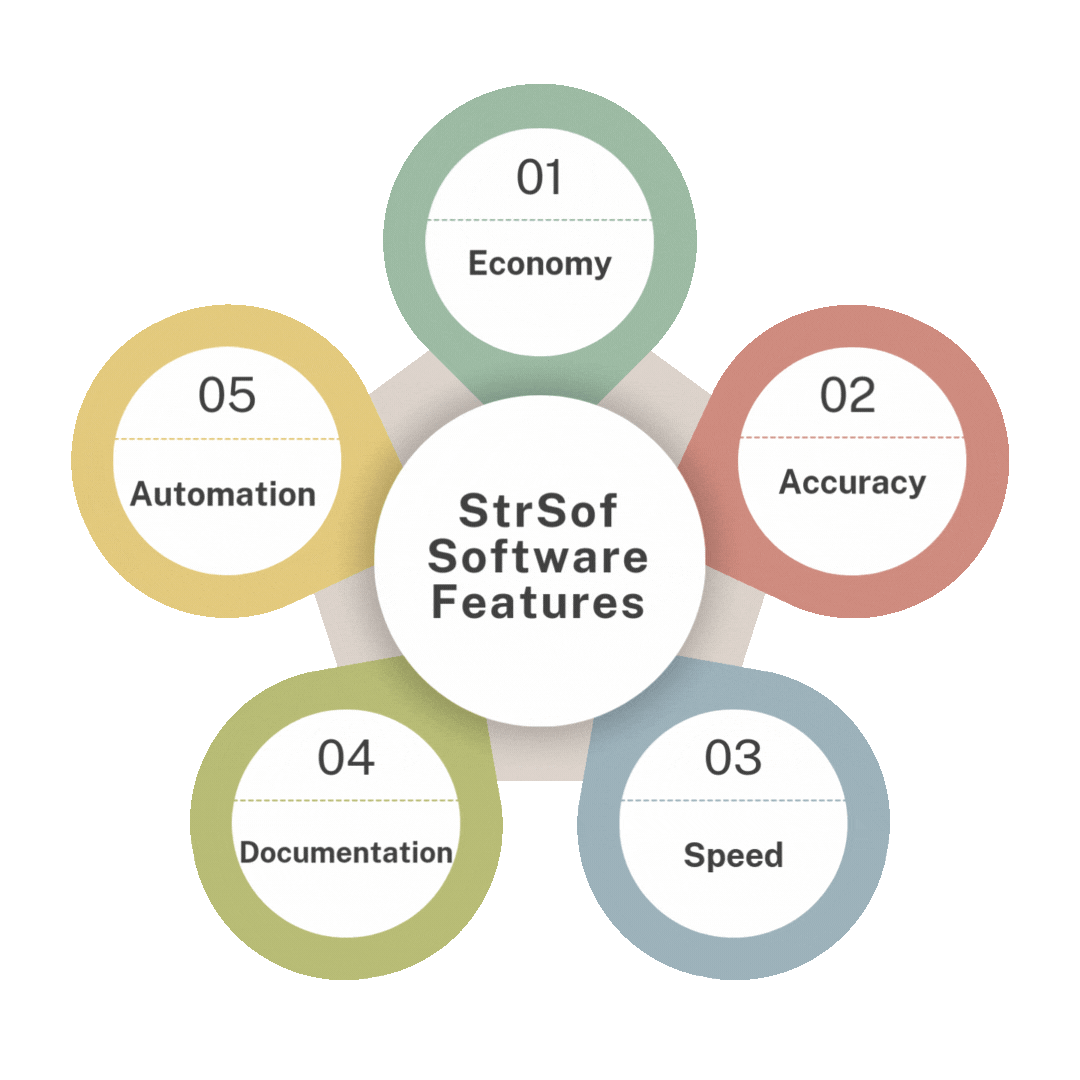
- Only the minimum dimensions and limiting ratios necessary for member design are needed as user input. The software autonomously calculates the final sizes.
- The results obtained are highly precise, and rounding-off of calculated values is aimed at providing conservative outcomes rather than leaning towards the unsafe side.
- The output includes step-by-step calculations with dynamic formulas and references to the design code, CAD drawing, bill of quantities (BOQ), and bar bending schedule (BBS).
- Utmost level of automation achievable for an engineering design template. Significantly streamlined with an intuitive user interface tailored for junior engineers, trainees, and newcomers.
- No prerequisite training is necessary to utilize these automated templates. User assistance is readily accessible on each input page for immediate support.
- Meticulously designed, maintained, and supervised by adept structural engineers hailing from prestigious institutions, boasting extensive expertise across diverse sectors.
- Adheres to rigorous design principles akin to those employed by the oil and gas industry.
Engineering hours are valuable. Avoid squandering them on repeatedly revising inputs using ‘Trial-And-Error’ templates.

Testimonials
What design engineers, construction personnel, academics, research scholars, and engineering students are sharing regarding our software/templates.
“It was only after I compared the results from your Spread Footing and Pedestal design software with those from other design tools that I fully embraced the concept of cost-effective engineering.”
Sundeep Reddy
(CMD – Zeromile Warehousing Ltd.)
“I’ve never encountered any problems with bolt tightening when using your baseplate design template for steel bases. It significantly cuts down on steel erection time too.”
A. Hameed
(Const. Manager – ANRI Developers)
“Although grasping the code and algorithms behind these automated templates may be challenging and intricate, using them is incredibly straightforward—even for an intern like me.”
H. Sohail
(PG Student – IIIT, Hyderabad)
“Many of these appear to be simple, user-friendly design templates but are, in fact, powerful civil engineering software.”
A. Hassan
(Civil Engineer)
“It’s truly remarkable to witness the array of optional pedestal and footing sizes, including the most cost-effective option, presented in the final output sheet after the design process”
Sunita Kulkarni
(Structural Engineer – Freelancer)
“The Baseplate software you provide has the potential to save hundreds of engineering manhours on every steel structure project it’s involved in.”
B. S. Reddy
(Engineering Manager – ECEPL)
“The Wind Load calculation template is excellent for gable-frame structures, delivering precise design wind pressures instantly.”
Pradeep Raj
(Sr. Engineer – Freelancer)
“By utilizing their design templates for RCC Pedestal and Spread Footing, we’ve managed to reduce foundation costs by nearly 20% on each project that involves shallow foundations.”
Subodh Mishra
(Group President – ZMW Projects Ltd.)
“The Load Combination Generator is a fantastic tool, even if you already have your own load combinations in a design file. However, it only accepts seven primary loads.”
Praneeth
(GET – Epicenter Consulting Engrs.)
“Designing stormwater drains becomes incredibly straightforward with this template, accommodating all three shapes of drains. It’s remarkably user-friendly and an invaluable asset in infrastructure design.”
K. Prabhakar
(MD – JSN Infra Consultants)
“Engaging in structural design with the software tools from StrSof.com is truly enjoyable, particularly those tailored for baseplate, pedestal, and footing designs.”
T. R. Kumar
(Ph.D. Scholar – IIIT, Hyderabad)
“The arrangement of rebar in the pedestal is highly precise and meaningful, ensuring accuracy in bar spacing, numbers, and perimeter spacing. It faithfully adheres to the provided input without fail.”
S. Rao
(Const. Manager)
“The Steel MTO application proves to be an excellent tool for any steel building project. It’s user-friendly, facilitates documentation, updates, and revisions effortlessly, and crucially, seamlessly transitions between estimators.”
K. Kartheek
(Sr. Estimator – Freelancer)
Get the best Structural Engineering Software
Blog Posts :
Learn in detail about best practices.
StrSof software achieves cost-effective designs for members like RCC pedestals and pad footings through a systematic and efficient process.The design begins with input parameters such as minimum dimensions and limiting aspect ratios. Using these inputs, the software generates numerous member sizes through exhaustive permutations of the member’s dimensions (three dimensions for footings and two for pedestals).For each generated size, design checks are conducted based on the selected design code. A member is deemed successful only if it satisfies the design criteria under all load combinations at all support joints.Finally, for all successful members, the software calculates costs by incorporating material rates for concrete, reinforcement bars, and formwork. The most cost-effective member size is identified as the one with the lowest calculated cost, ensuring both structural integrity and economic efficiency. [...]
Read more...
The cost of a structural member, such as an RCC pedestal or spread footing, is primarily influenced by the costs of concrete, reinforcement bars, and formwork. Unless the design template or software accounts for the material rates of these components, achieving a cost-effective design is unlikely.Unlike traditional “hit-and-trial” methods, StrSof software integrates the material rates for concrete, reinforcement bars, and formwork directly into the design process. This ensures the most economical member size is selected. The effectiveness of this approach is evident in the final output sheet, which lists all possible member sizes along with their costs. [...]
Read more...
The main difference between a stiffened baseplate and an unstiffened baseplate lies in their structural design and ability to resist bending moments and shear forces:
Stiffened Baseplate: This type of baseplate includes additional stiffeners, typically in the form of ribs or gussets welded to the plate. These stiffeners enhance the baseplate’s rigidity and ability to transfer loads more efficiently between the column and the foundation. Stiffened baseplates are commonly used when the column imposes significant bending moments or shear forces onto the baseplate, requiring additional stiffness to prevent excessive deflection or failure.
Unstiffened Baseplate: An unstiffened baseplate lacks these additional stiffeners. It is typically used in situations where the column loads are relatively lighter and do not induce significant bending moments or shear forces. Unstiffened baseplates are simpler in design and fabrication, often suitable for smaller or less demanding structural applications where the forces are adequately managed without the need for additional stiffening elements.
In summary, while both types serve to anchor columns to foundations, stiffened baseplates provide enhanced stiffness and load transfer capabilities, whereas unstiffened baseplates are simpler and sufficient for lighter loads and less demanding structural conditions. [...]
Read more...
Pad footings (also known as spread footings) are indeed one of the most common types of foundations used in construction, particularly for smaller to medium-sized buildings and structures. They are characterized by their relatively simple design, consisting of a single, thick concrete slab that usually supports the load from a single column. Pad footings distribute the structural loads from supported column to the soil underneath, providing stability and preventing excessive settlement.
For larger buildings or structures with heavier loads, other types of foundations like strip footings, raft foundations, or piles may be more suitable. Each type of foundation has its advantages and is chosen based on factors such as load distribution, soil bearing capacity, settlement control, and construction feasibility. Therefore, while pad footings are widespread, their prevalence varies depending on specific project needs and conditions. [...]
Read more...
Yes, a fully automated engineering design template is possible and increasingly feasible with advancements in artificial intelligence (AI) and machine learning (ML). Such templates leverage algorithms to automate the entire design process, from initial concept generation to detailed optimization and validation.
Key components of a fully automated design template include:
AI-Driven Concept Generation: Algorithms can generate and evaluate numerous design concepts based on input criteria and constraints, surpassing human capabilities in exploring a vast design space.
Optimization Algorithms: ML algorithms can optimize designs iteratively, improving performance metrics such as efficiency, cost-effectiveness, or reliability based on real-time feedback.
Simulation and Validation: Automated templates can simulate and validate designs using virtual testing environments, predicting real-world performance and behavior accurately.
Iterative Learning: By learning from previous designs and outcomes, automated templates continuously improve and refine their design processes.
While challenges such as complexity, integration with existing systems, and ensuring reliability remain, ongoing research and development are pushing the boundaries of what fully automated engineering design templates can achieve, promising significant efficiency gains and innovative solutions across industries. [...]
Read more...
A standalone engineering design template offers several advantages over full-fledged software, particularly in specific contexts or for certain types of projects:
Simplicity and Accessibility: Standalone templates are often simpler to use and require less technical expertise compared to complex engineering software. This accessibility allows engineers with varying levels of experience to quickly implement and iterate on designs.
Cost Effectiveness: Templates are generally more cost-effective, especially for smaller projects or when budget constraints limit the use of expensive software licenses. They provide essential design functionalities without the overhead costs associated with comprehensive software packages.
Customizability: Engineers can customize templates to suit specific project requirements or industry standards. This flexibility allows for tailoring designs without the need for extensive programming or customization efforts often required in full-fledged software.
Speed of Implementation: Standalone templates often facilitate quicker implementation of design ideas, as they typically focus on specific design tasks without the complexity of comprehensive software features. This speed can be crucial for rapid prototyping or when quick design iterations are necessary.
Offline Capability: In situations where internet access or connectivity is limited or unreliable, standalone templates offer the advantage of offline usability, ensuring continuity of work without dependency on external servers or cloud-based solutions.
These benefits make standalone engineering design templates a practical choice for certain applications where simplicity, cost efficiency, and customization are prioritized over the extensive capabilities of full-fledged engineering software. [...]
Read more...
A “hit-and-trial” engineering design template typically involves a more manual and iterative approach to engineering design. This process is often characterized by a trial-and-error approach, where multiple iterations may be required to achieve the desired outcome. It involves a hands-on, sometimes intuitive process where adjustments are made based on immediate results and observations.
In contrast, engineering software provides a more systematic and computerized approach to design. It often incorporates advanced algorithms, simulations, and modeling techniques. Engineering software allows for precise calculations, detailed analysis, and optimization based on mathematical models and simulations. [...]
Read more...